Features of PSA/VPSA Oxygen Plants
Usually the design of PSA oxygen plants relies on many factors such as:
- Zeolite bed packing
- Bed length
- Diameter
- Rate of in-feed air
In large sized PSA plants, the PSA process is only cost effective while operating at maximum separation efficiency. We are manufacturing PSA / VPSA Oxygen Producing Plants. The Oxygen Generator works on Pressure Swing Adsorption Principle using molecular silver. Upstream Equipment for Feed Air required for oxygen generator is not available from your centralized air supply you will be required to attach the feed air compressor. Downstream Equipment for Oxygen Generator For Oxygen required in hospitals, Bacteria filters are provided.
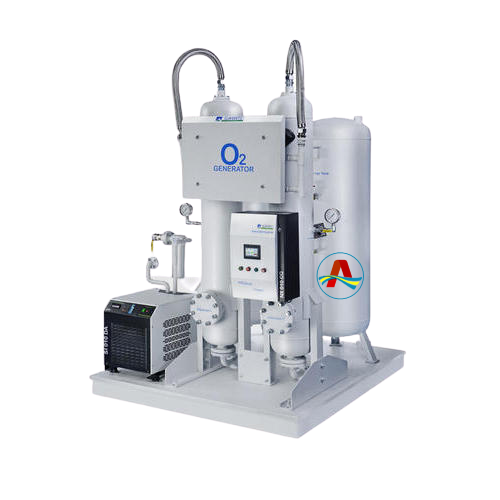
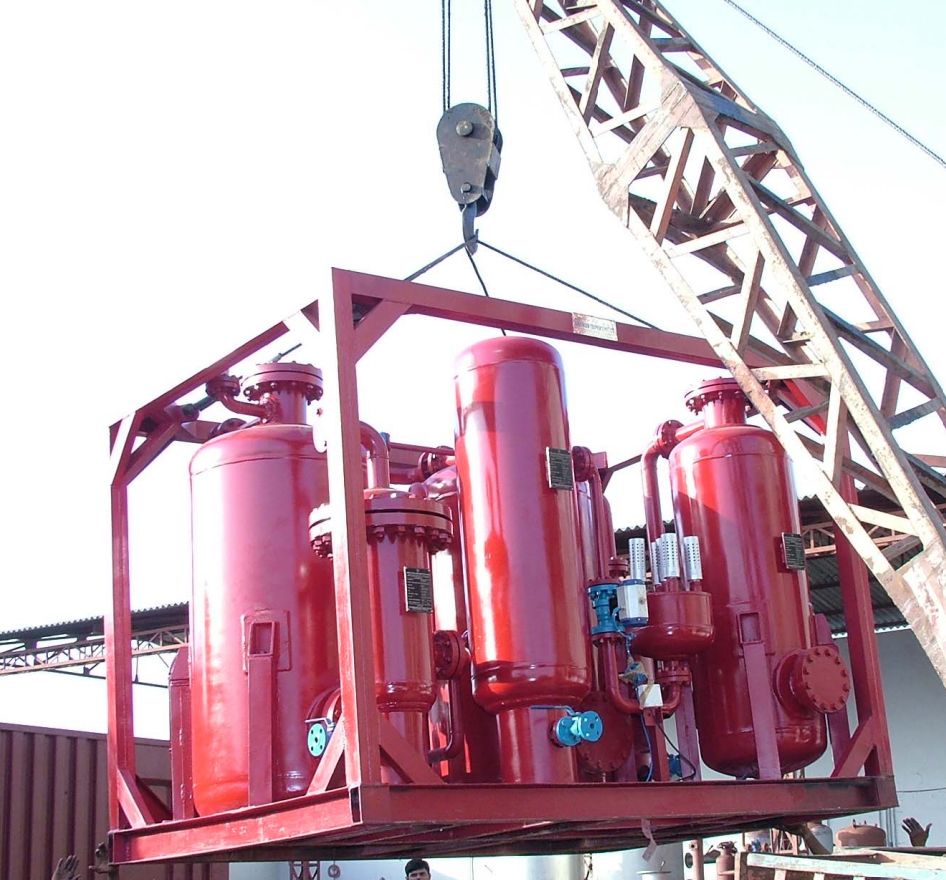
Applications of PSA/VPSA Oxygen Plants
Ferrous metallurgy: For electric furnace steel making, blast furnace iron making, cupola oxygen blasting and heating and cutting, for lancing in steel Industries, etc.
Non-ferrous metal refinery: It can improve productivity and reduce energy cost, also protect our environment.
Water process: For oxygen aeration active mud processes, reservation off surface water. Fishes breed aquatics, industrial oxidation process, and humid oxygenation, Effluent & waste water treatment.
Others: Pulp and paper industry, Chemical industry production, solid garbage burning, concrete production, glass manufacturing, medical oxygen, Biotechnology industry, Steel industry, Color and B&W picture tube/glass shell Industry, Lamp/ compact fluorescent lamp Industry, Vials & ampoules, Brazing application, Fish farming, Ozone Generation, LPC enrichment.
Benefits of PSA/VPSA Plants
Compared to other processes, the PSA process has certain features
1. Full Automation All systems are designed for un-attended operation and automatic Oxygen demand adjustment, Low Pressure drop, high output pressure, touch screen panel, Digital flow meters and purity analyzers.
2. Lower Space Requirement The design and Instrumentation makes the plant size very compact, assembly on skids, prefabricated and supplied from factory, Short installation period and small ground treatment workload.
3. Fast Start-up Start-up time is only 15 minutes to get desired Oxygen purity. So these units can be switched ON & OFF as per Oxygen demand changes. Production Attained within 10-15 minutes.
4. High Reliability Very reliable for continuous and steady operation with constant Oxygen purity. Plant availability time is better than 99% always. Purity up to 95% is easily achievable. It is Independent of on-site production. Also it has High operational efficiency. Full Safety, No hazards involved as with bulky gas cylinders.
5. Molecular Sieves Life Expected Molecular sieves life is around 15-years i.e. whole life time of Oxygen plant. So no replacement costs.
6. Low Production Cost Low investment and energy consumption, Low capital & running cost, simple operation and maintenance.
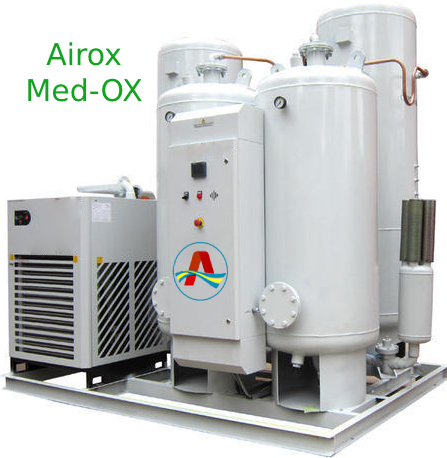
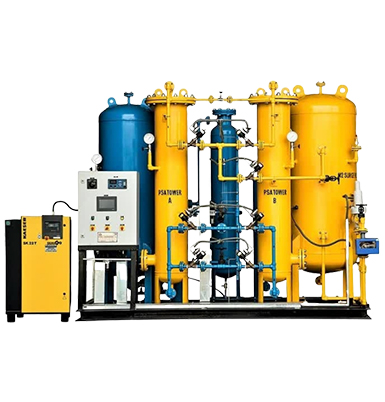
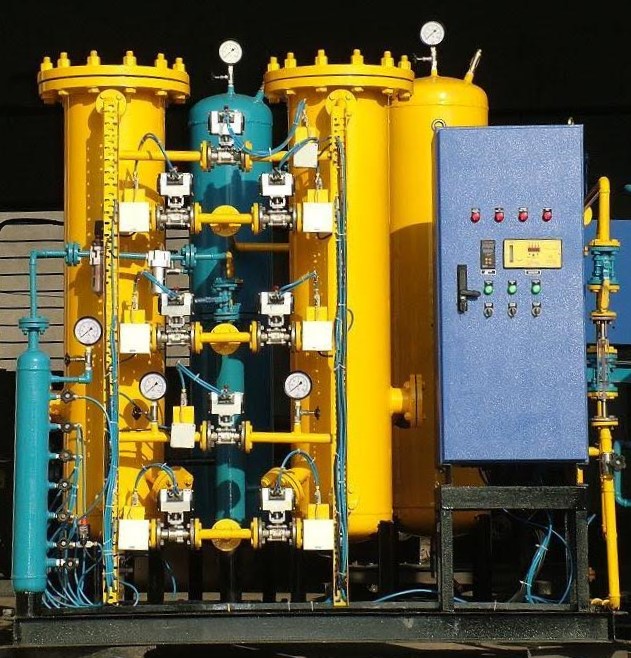
Standard Scope of Supply
- Air intake after cooler, moisture separator, pre-filter, audio drain valve & wet air receiver
- Twin tower desiccant based air dryer fully automatic with pneumatically operated changeover-valves.
- Dry air receiver with pressure gauge, pressure switch and candle type after filter.
- Twin tower P.S.A. Module with automatic pneumatically operated changeover valves, pressure gauges & interconnecting piping.
- Surge Vessel with instruments & drain Valve.
- Z.M.S. (Zeolite Molecular Sieves) one charge filled in P.S.A. Adsorption Towers.
- Flow meters for oxygen with flow control valve, NRV and Back pressure Controller.
- Centralized control panel with sequence programmer and fault Indications Lamps.
- Online Oxygen Analyzer with settable low oxygen and very low oxygen alarms.